Bir endüstri mühendisi olarak, iş hayatımda en çok önemsediğim konulardan biri verimliliktir. Danışmanlık kariyerim sırasında kurumsallaşma sürecini yönettiğim şirketlerde, sürecin zorunlu kılmadığı durumlarda bile verimliliği sağlamaya ve kârlılığı arttırmaya dönük çalışmalarımız olmuştur.
Kavramlar
Ölçmeden yönetemeyeceğimize göre verimliliği arttırmanın tek yolu, iş süreçlerini belirlemek ve işleyişteki darboğaz ve israfları ortadan kaldırmaktır. Tam burada da “İş Süreci Değişim Mühendisliği (Business Process Reengineering)” kavramı gündeme gelmektedir.
İş süreci değişim mühendisliği, “Simülasyon” ve “Optimizasyon” gibi endüstri mühendisliği araçları ile birleştiğinde verimliliğin ölçümü ve arttırılması için kapı da aralanmaktadır.
Lütfen sıkılmayın, bu iki kavramın tanımından bahsetmem gerekiyor.
Simülasyon gerçek bir sistemin modelini tasarlayarak, davranışını anlamak veya değişik stratejileri değerlendirmek amacı ile bu model üzerinde denemeler yapmaktır.1
Optimizasyon ise bir sistemde bulunan (işgücü, zaman, sermaye, hammadde, kapasite ve donanım gibi) kaynakların en verimli şekilde kullanılarak maliyetin minimize edilmesi, kârın ve kapasite kullanımının maksimize edilmesi gibi amaçlara ulaşılmasını sağlayan bir tekniktir.2
İş süreci değişim mühendisliği nasıl uygulanır?
Konu, üzerinde çok sayıda akademik çalışmanın yapıldığı ve pek çok işte uygulama alanı bulan bir ayrıntıdadır. Ancak size bu metodolojiyi bir blog yazısının olabileceği sadelikten uzaklaşmadan, basit bir örnekle anlatmaya çalışacağım.
Bir Örnek: “Tişört Üretimi”
Basit olmasını istediğim örneğimi, tekstil mühendisi ve öğretim görevlisi olan Alime Aslı İlleez’in yüksek lisans tezinden aldım. Örneğe ait akış basamakları ve ölçümler ile yazarın farklı bir metotla yaptığı hat dengeleme çalışması, tezinin 61’inci sayfasında yer alıyor.3 Ben oradaki iş akışını, aşağıdaki şemada görüldüğü gibi haritaladım:
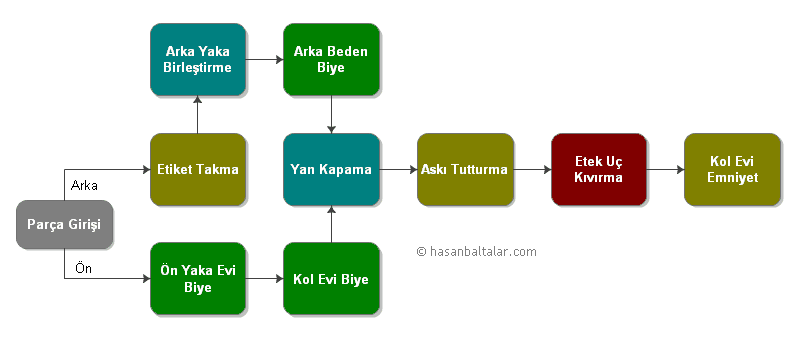
Örnek modelimiz nasıl çalışıyor?
Sürecin girdisi, tişörtün kesilmiş ön ve arka parçalarından oluşuyor. Dokuz saatten oluşan bir günlük çalışmada, 800 tişörtlük toplam 1600 parça iki ayrı işleme giriş yapıyor. Ön ve arka parçalar, ayrı sürelerle ayrı işlemlerden geçerek, “Yan Kapama” işleminde buluşuyor ve birleşerek dikilmiş tişört haline geliyor.
Yan kapama işleminde bir ayrıntı var: Buraya her bir akışta ilk gelen parça, bütünleşebilmek için eş parçasını bekliyor. Modellemede bunu göz ardı etmemek gerekiyor.
Üretimde dört çeşit makine kullanılıyor. Şemadaki kutuların renkleri, işlemlerin yapıldığı farklı makineleri ifade ediyor.
Sorumuz ise şu: “Günlük 800 adet olan siparişi karşılayabilmek için, elimizdeki kesilmiş malzemeleri ürüne dönüştürecek makinelerden kaçar adede ihtiyacımız var?”
Şimdi, modelimizi çalıştırmaya başlayalım.
Senaryo ve Simülasyonlar
İş süreci değişim mühendisliği gereği yapacağımız simülasyonları, birer senaryo ile kurguluyoruz. Her bir senaryoda yeni bir ortamın değişkenlerini tanımlıyor ve simülasyona geçiyoruz.
Örnek tişört üretimimiz için dört farklı makineye ihtiyacımız var. O nedenle ilk ve temel senaryomuzu, her makineden mecbur olduğumuz birer adet ile kuruyoruz. Daha sonra da modelimizi çalıştırıyoruz. (Örneğimiz yeni hat kurulumu gibi görünmese ve soru da “Hattımız kurulu ve çalışıyor ama bir türlü siparişi karşılayamıyoruz. Ne yapmalıyız?” şeklinde sorulsaydı, ilk senaryomuzu kurulu düzen üzerine oluşturacaktık.)
Simülasyonlar, dört ana kategoride çıktı verirler. Bunlar zaman, maliyet, kaynaklar ve kuyruklardır. Bu çıktılardaki bilgiler, yeni senaryomuzu kurgulamaya yarar. Amacımız doğrultusunda kimi işlerde zamana, kimisinde maliyetlere odaklanmamız gerekir. Biz bu örnek için kaynaklara göz atıyoruz.
Örneğimizdeki ilk simülasyonda, kaynak kullanımı hakkındaki aşağıda bulunan bilgileri elde ediyoruz:
Kaynak Miktarı (adet) | S-1 |
---|---|
Düz Dikiş Makinesi | 1 |
Dört İplik Overlok Makinesi | 1 |
Bant Reçme | 1 |
Reçme | 1 |
Kaynak Kullanımı (%) | S-1 |
Düz Dikiş Makinesi | 99,78 |
Dört İplik Overlok Makinesi | 99,85 |
Bant Reçme | 100,00 |
Reçme | 23,79 |
Çıktı Miktarı (adet) | S-1 |
Tişört | 236 |
Üretimde reçme makinesini ancak %23,79 kapasite ile kullanabildiğimiz ve tüm gün 800 adetlik girdi ile 236 adet tişört üretebildiğimizi görüyoruz.
Bu durumda, reçme dışında kalan ve darboğaz oluşturan makinelerin sayısını arttırmamız gerekiyor. Kullanım oranları birbirine çok yakın olduğundan, üçünü de birer adet arttırıp, ikinci senaryomuzu kurguluyor ve tekrar simüle ediyoruz.
Kaynak Miktarı (adet) | S-1 | S-2 |
---|---|---|
Düz Dikiş Makinesi | 1 | 2 |
Dört İplik Overlok Makinesi | 1 | 2 |
Bant Reçme | 1 | 2 |
Reçme | 1 | 1 |
Kaynak Kullanımı (%) | S-1 | S-2 |
Düz Dikiş Makinesi | 99,78 | 89,58 |
Dört İplik Overlok Makinesi | 99,85 | 99,79 |
Bant Reçme | 100,00 | 88,49 |
Reçme | 23,79 | 67,54 |
Çıktı Miktarı (adet) | S-1 | S-2 |
Tişört | 236 | 700 |
Reçme makinesinden faydalanma oranını %67,54’e çıkardık, üretilen tişört sayısı da 700’e yükseldi. Darboğaz, sadece dört iplik overlok makinesinde kaldı. Üçüncü senaryomuzda da onun sayısına bir adet ekleme yapıyoruz.
Kaynak Miktarı (adet) | S-1 | S-2 | S-3 |
---|---|---|---|
Düz Dikiş Makinesi | 1 | 2 | 2 |
Dört İplik Overlok Makinesi | 1 | 2 | 3 |
Bant Reçme | 1 | 2 | 2 |
Reçme | 1 | 1 | 1 |
Kaynak Kullanımı (%) | S-1 | S-2 | S-3 |
Düz Dikiş Makinesi | 99,78 | 89,58 | 97,43 |
Dört İplik Overlok Makinesi | 99,85 | 99,79 | 73,92 |
Bant Reçme | 100,00 | 88,49 | 90,32 |
Reçme | 23,79 | 67,54 | 76,63 |
Çıktı Miktarı (adet) | S-1 | S-2 | S-3 |
Tişört | 236 | 700 | 795 |
Reçme makinesinden faydalanma oranı bu kez %76,63’e, tişört sayısı da 795’e yükseldi. Darboğaz bu kez düz dikiş makinesine geçti. Dördüncü senaryomuzda da onun miktarına bir adet ekleme yapalım.
Kaynak Miktarı (adet) | S-1 | S-2 | S-3 | S-4 |
---|---|---|---|---|
Düz Dikiş Makinesi | 1 | 2 | 2 | 3 |
Dört İplik Overlok Makinesi | 1 | 2 | 3 | 3 |
Bant Reçme | 1 | 2 | 2 | 2 |
Reçme | 1 | 1 | 1 | 1 |
Kaynak Kullanımı (%) | S-1 | S-2 | S-3 | S-4 |
Düz Dikiş Makinesi | 99,78 | 89,58 | 97,43 | 64,96 |
Dört İplik Overlok Makinesi | 99,85 | 99,79 | 73,92 | 73,92 |
Bant Reçme | 100,00 | 88,49 | 90,32 | 90,32 |
Reçme | 23,79 | 67,54 | 76,63 | 76,65 |
Çıktı Miktarı (adet) | S-1 | S-2 | S-3 | S-4 |
Tişört | 236 | 700 | 795 | 795 |
Fakat o da ne? Görüleceği üzere, üç makinenin kaynak kullanım oranında ve günlük üretim sayısında bir değişiklik olmadığı gibi, son senaryoda sayısını arttırdığımız düz dikiş makinesinden faydalanma oranı da azaldı.
Ulaştığımız Nokta: “En İyi (Optimal) Değerler”
Ulaştığımız Nokta:
“En İyi (Optimal) Değerler”
Tişört üretimi örneğimizde, kurguladığımız dört senaryonun üçüncüsü ile üretim sürecini optimize ettiğimiz ve en iyi değerleri yakaladığımız anlaşılıyor. Bundan sonra, bu modeli gerçek üretim yerinde uygulamak kalıyor.
Sadece üretim mi?
Kolay algılanabildiğinden, bu yazı için örneği üretim alanından seçtim. Ancak iş süreci değişim mühendisliği, sadece üretim alanında işe yarayan bir metodoloji değildir. Akışı haritalanabilen, kaynakları ve işlem zamanları tespit edilebilen her yerde bu çalışma yapılabilir. Geçmişte üç kişi çalıştırdığı halde hastaların dakikalarca beklemek zorunda bırakıldığı bir eczacı arkadaşım, gözlemleriyle süreçlerde bir aksaklık olduğunu zezmiş ve bir iyileşme yapıp yapamayacağımızı sormuştu. Dünyada bu tip çalışmalarla milyonlarca liralık tasarrufun yapıldığı örnekler mevcuttur.
Davet
Bu yazımı okuyan iş insanlarını, konuyla ilgilenmeye ve kaynakların verimli kullanımı için içinde bulundukları iş süreçlerini optimize etmeye davet ediyorum. Bugünlerde ekonominin ne kadar sıkıntılı olduğu malumunuzdur. Maliyeti azaltıp kârı arttırmak, kaynakları verimli kullanmak elzemdir.
Sorunuz olursa, benimle iletişim kurmaktan lütfen çekinmeyiniz.
- Halaç, Osman. “İşletmelerde Simülasyon Teknikleri” (1982)
- Elektrik Port. “Mühendislikte Optimizasyon” (12.12.2016) elektrikport.com
- İlleez, Alime Aslı. “Konfeksiyon Sektöründe Süreç Planlamasında Kullanılabilecek Matematiksel Yöntemler” (15.12.2006) acikerisim.ege.edu.tr
Yorumunuzla katkıda bulunun